Fasteners and Machining: Important Components for Precision Manufacturing
Grasping the Art of Fasteners and Machining: Advancements and Ideal Practices
In the world of commercial manufacturing and engineering, the proficiency of fasteners and machining is a cornerstone of making certain architectural honesty, performance, and longevity in various applications. As technology breakthroughs and demands for effectiveness and accuracy increase, staying abreast of the current innovations and finest methods in attachment and machining ends up being vital. From the evolution of securing technologies to the details of choosing one of the most ideal products, the landscape of modern manufacturing is continuously progressing. Join us as we explore the most up to date developments and dig into the nuanced globe of mastering fasteners and machining, revealing key understandings and approaches that can boost your strategy to design options.
Advancement of Fastening Technologies
Throughout the industrial transformation and into the contemporary period, the evolution of fastening modern technologies has been marked by continuous improvements in efficiency and integrity. Bolts, such as screws, rivets, and screws, play a critical duty in different markets, including auto, aerospace, building, and electronic devices. The requirement for more powerful, more durable, and easier-to-install attachment solutions has actually driven development in the field.
One considerable growth has actually been the shift towards accuracy machining methods to create fasteners with greater resistances and premium performance. This change has made it possible for makers to generate fasteners that satisfy stringent high quality requirements and deal boosted resistance to deterioration and exhaustion.
Additionally, the introduction of innovative products, such as titanium alloys and compounds, has actually revolutionized the capabilities of fasteners. Fasteners and Machining. These materials give outstanding strength-to-weight proportions, making them excellent for applications where reducing weight is essential without endangering architectural integrity
Developments in Machining Methods
In the world of commercial manufacturing, the continuous evolution of machining methods has actually led the method for extraordinary accuracy and performance in the manufacturing of bolts. Among the substantial advancements in machining methods is the application of Computer Numerical Control (CNC) innovation. CNC devices supply unmatched precision and repeatability by enabling for automated control of machining devices. This accurate control allows suppliers to develop complicated and complex fastener layouts easily.

In addition, the adoption of multi-axis machining facilities has actually made it possible for simultaneous cutting procedures from different angles, even more enhancing performance and decreasing manufacturing times. By making use of these sophisticated machining methods, makers can meet the boosting need for premium bolts while keeping cost-effectiveness in their procedures.
Choosing the Right Fastener Materials
Picking the ideal material for bolts is a crucial decision that significantly influences the performance and long life of the put together components. When choosing the ideal fastener material, a number of aspects should be considered to make sure the longevity and integrity of the end product. The material selected need to work with the environmental problems the fasteners will certainly be revealed to, such as temperature variants, moisture degrees, and harsh components.
Common products used for fasteners consist of stainless-steel, carbon titanium, light weight aluminum, and steel, each offering special residential properties that match different applications. Stainless steel, for instance, is understood for its rust resistance, making it perfect for marine or outdoor settings. Carbon steel is a cost-efficient option appropriate for numerous general-purpose applications. Light weight aluminum is lightweight and often used in markets where weight is a vital variable. Titanium, on the other hand, is extremely strong and corrosion-resistant, making it ideal for high-performance applications.
Enhancing Precision in Machining
Attaining optimal precision in machining is vital for making certain the quality and efficiency of machined parts. To boost precision in machining, suppliers employ a range of innovative strategies and technologies.
In addition to CNC machining, using advanced cutting tools and device owners can also considerably enhance accuracy. Top quality cutting tools with sophisticated coatings decrease rubbing and wear, bring about Continue extra accurate cuts and dimensional precision. Moreover, carrying out strict quality control actions throughout the machining procedure, such as normal inspections and calibration of tools, aids maintain constant accuracy degrees. By focusing on accuracy in machining, manufacturers can accomplish exceptional item high quality, tighter tolerances, and enhanced general efficiency of machined components.
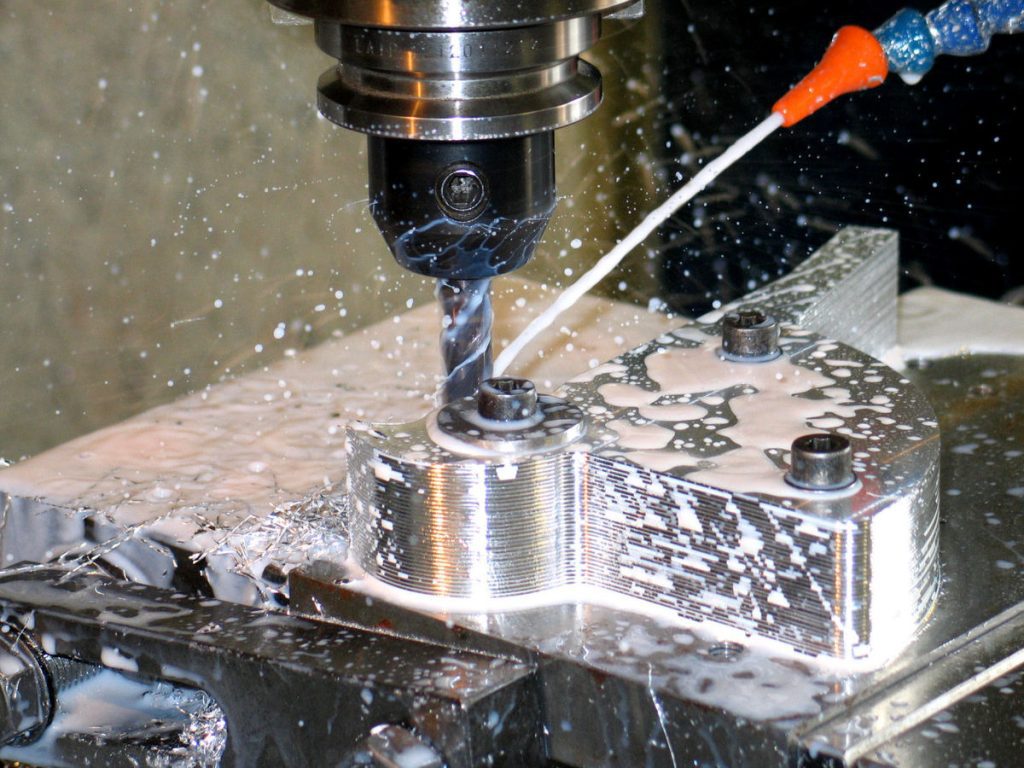
Best Practices for Bolt Installment
Precision in machining plays a vital function in guaranteeing the dependability and long life of fastener setups. When it comes to best techniques for fastener installment, one essential facet is the proper choice of fasteners based upon the specific application requirements. Utilizing the right type, dimension, and material of bolt is necessary to assure ideal performance and longevity. Fasteners and Machining. In addition, it is paramount to adhere to maker standards and advised torque worths throughout the installment procedure to stop under-tightening or over-tightening, which can cause early fastener failure.
Moreover, guaranteeing that the bolt strings are complimentary and clean of debris prior to setup is crucial to achieving a safe and reliable connection. Utilizing thread-locking substances or washers can likewise enhance the stability of the bolt assembly. Routine examinations and upkeep of fasteners post-installation are advised to recognize any kind of potential problems early and prevent pricey repairs or replacements in the future. By sticking to these ideal methods, suppliers can maximize the stability and performance of their bolt installments.
Conclusion
By selecting the ideal fastener products and boosting precision in machining, manufacturers can achieve optimal results in their procedures. Overall, understanding the art of bolts and machining involves continual technology and adherence to finest methods.
In the realm of industrial you could try these out manufacturing, the continuous evolution of machining methods has paved the method for extraordinary accuracy and efficiency in the production of bolts.Precision in machining plays a vital role in making certain the integrity and longevity of fastener installations. When it comes to finest techniques for fastener installation, one vital element is the correct option of fasteners based on the particular application requirements. By choosing the best fastener materials and boosting accuracy in machining, manufacturers can achieve optimal outcomes in their operations. Generally, grasping the art of fasteners and machining includes look these up continual development and adherence to ideal techniques.